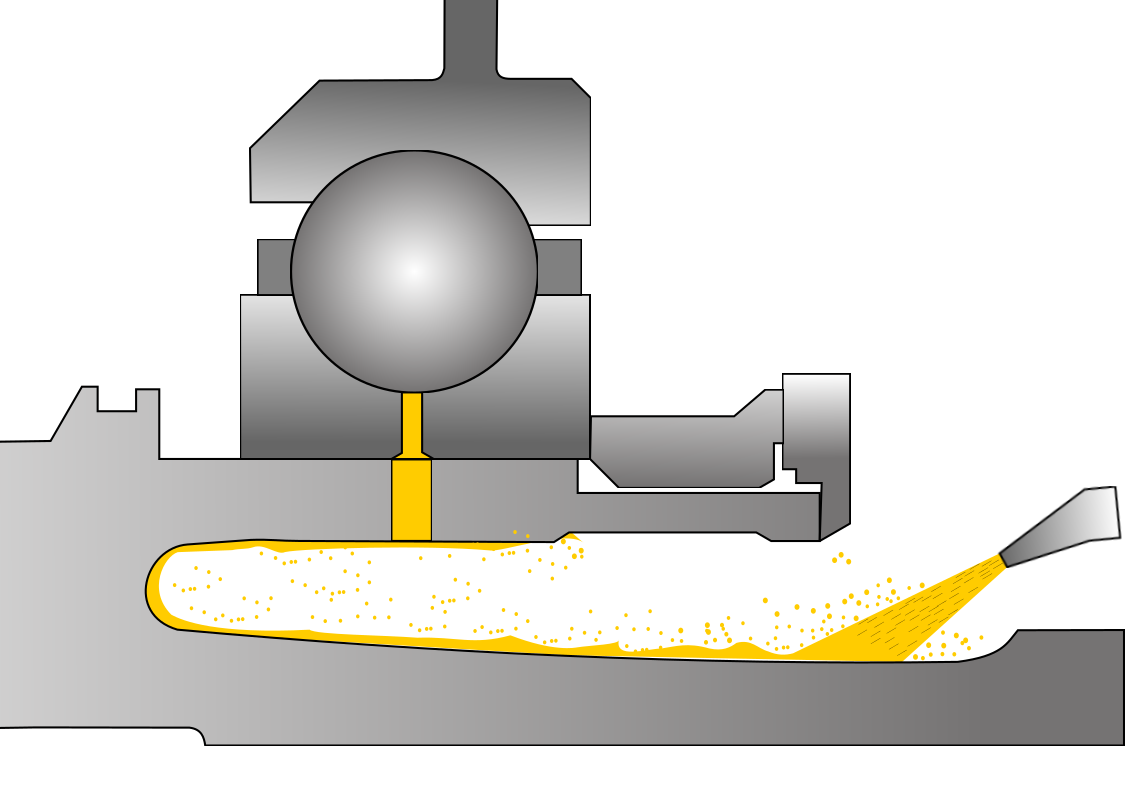
Optimization of the oil supply in engine storage chambers
- Contact:
- Project Group:
Air and Oil System
Overview
An efficient oil system is required to reliably supply oil for lubrication and, above all, cooling to all the gearboxes and bearings of an engine. Due to their good emergency running properties, roller bearings are used to support the shafts and ensure that the engine shafts are suspended. The oil for lubricating the bearing is fed into the bearing chambers via oil nozzles. In addition to other supply strategies, under-race lubrication is used as an effective and safe method of cooling. For this purpose, the oil is fed via a nozzle, as shown in Figure 1, onto the engine shaft and from there through the inside of the rotor to the underside of the bearing seat.
Figure 1: Oil supply to bearing chamber via nozzle
To increase the efficiency of the engine, it is necessary to optimize the supply of oil to the rolling bearing to improve cooling and lubrication while minimizing power loss. Therefore, a deeper understanding of the oil supply as well as oil distribution, oil demand and interaction between fluid and shaft is required for the development of new concepts with different geometries.
At ITS, the oil supply in a typical engine bearing chamber is investigated using experimental and numerical methods.
For the experimental investigation of the oil supply to the bearing, a modular test rig (Figure 2) is used at the institute, with which different configurations and geometries can be tested. Different operating conditions can be created in the test rig in order to investigate the influence of important operating parameters on the oil distribution and temperature distribution at the bearing. The influencing parameters that are determined in the test bench are
- Oil temperature
- rotational speed
- Axial load on bearing
- Injection angle
- Oil flow
A multiphase smoothed particle hydrodynamics (SPH) method is used for the numerical investigation of the oil supply. The aim of the investigation is to describe the following aspects:
- Evaluation of the oil distribution
- Characterization of the efficiency of the oil system under different operating conditions
- Quantification of the uniformity of the oil distribution
- Evaluation of different geometries that allow better oil lubrication
Figure 3: Incident oil jet