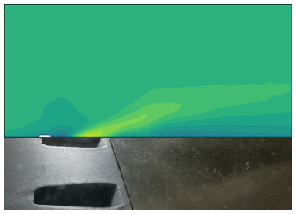
Film cooling in gas turbines and aircraft engines
- Contact:
- Project Group:
Heat transfer and cooling methods.
Optimization of film cooling
The principle of film cooling in aircraft engines and stationary gas turbines is the main reason for the high combustion chamber and turbine inlet temperatures of up to 2000K. Continuous improvement of film cooling therefore enables further increases in turbine inlet temperatures and thus contributes to an increase in thermal efficiency. During film cooling blow-out, flow separation, complex vortex systems and shear layers occur at the inlet to the film cooling bore, as well as in the bore and at its outlet, which have an enormous influence on the effectiveness of the film cooling blow-out. Depending on the operating point of the gas turbine, i.e. the flow conditions on the cooling air and hot gas side, as well as the position of the bore in the blade geometry, very different aero-thermal conditions arise for the same bore geometry.
For a better understanding of the aero-thermal behavior of different bore geometries and the cooling air-hot gas interaction at the cooling air bore outlet, experimental investigations (on the film cooling test rig, Fraas et al. [1]) are carried out at the Institute of Thermal Fluid Machinery (ITS). Using Stereo Particle Image Velocimetry (SPIV), a laser-optical measuring technique, all velocity components can be determined in a measuring plane - for example in the interaction area between cooling air and hot gas. In addition, infrared thermography (IRT) is used to determine the temperature distribution downstream of the film cooling bore. By applying the superposition principle according to Choe et al [2], the film cooling parameters "adiabatic film cooling effectiveness" and "heat transfer coefficient with film cooling" can be determined by means of two measurements of different thermal boundary conditions.
Objectives in the research area of film cooling at ITS
- Identification of dominant flow structures of the cooling air-hot gas interaction (e.g. using methods of dimensional reduction, POD, DMD)
- Robust design of film cooling bore geometries
- Further development of reliable and precise measurement technology to determine the derived film cooling variables and the flow field
Film cooling efficiencies from measurements using IRT
The adiabatic film cooling effectiveness (in combination with the heat transfer coefficient with film cooling) is used to evaluate different hole geometries in comparison to each other. Shown is the adiabatic film cooling effectiveness downstream of the blow-out point (left) for a high cooling air channel Reynolds number, as well as a lateral distribution of the effectiveness (center) and the laterally averaged course of the film cooling effectiveness along the flow direction downstream of the blow-out point (right) for a high and a low cooling air channel Reynolds number respectively. The hole is a classic diffuser hole with a cooling air cross-flow orthogonal to the hot gas. The "film cooling footprint" is therefore asymmetrical and varies greatly depending on the blow-out rate (M) and cooling air duct Reynolds number (Fraas 2019 [3]).
Velocity fields from measurements using SPIV
The magnitude of the mean absolute velocity in the wall-normal plane in the flow direction centered above the bore outlet determined using SPIV is shown in the figure for the blow-out rate M = 3. By analyzing all velocity components, stationary vortex systems as well as unsteady vortex systems can be detected.
Sources:
[1] Fraas, M., Glasenapp, T., Schulz, A., and Bauer, H.J., 2017. "Introducing a New Test Rig for Film Cooling Measurements with Realistic Hole Inflow Conditions". In Proceedings of ASME Turbo Expo 2017, no. GT2017-63585. ISBN 978-0-7918-5089-3
[2] Choe, H., Kays, W. M., and Moffat, R. J., 1974. "The Superposition Approach to Film-Cooling". In Proceedings of ASME Winter Annual Meeting 1974.
[3] Fraas, M., 2019: The influence of the inlet geometry on the cooling effect of a contoured film cooling bore with cross-flow on the cooling air side, vol. 78 of Forschungsberichte aus dem Institut für Thermische Strömungsmaschinen / Universität Karlsruhe (TH). Logos-Verlag, Berlin. ISBN 9783832549701.